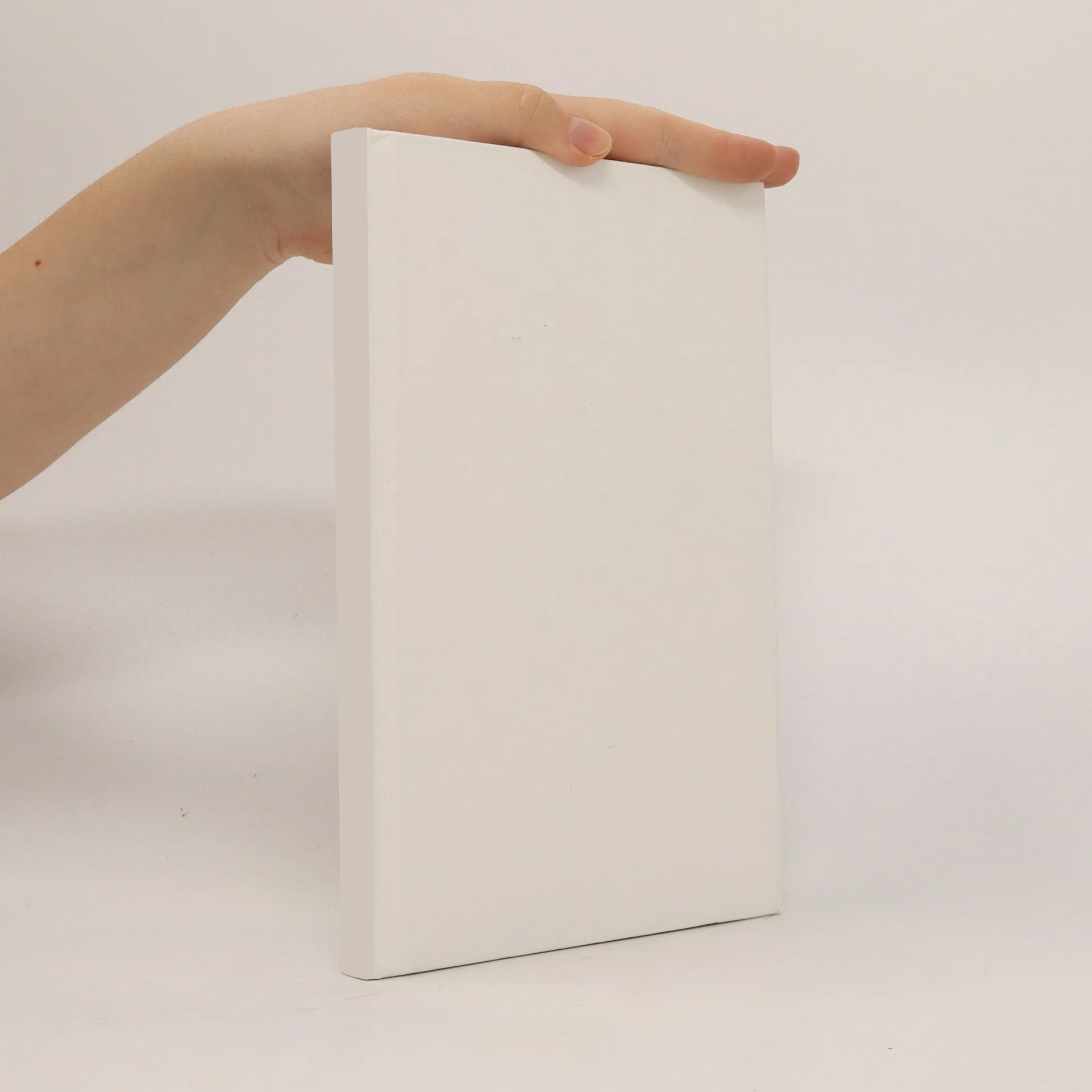
Viac o knihe
The predicted shortage of fossil fuels is likely to have a negative influence on the availability of base chemicals, like propylene required to produce important derivatives like n-butanol. The resulting increase in oil price and demand in C4 chemicals provides a good and necessary foundation for alternative biochemical production routes. Biobutanol production, through the anaerobic fermentation of Clostridium acetobutylicum and Clostridium beijerinckii bacteria has seen great research interest due to the recognizable potential of butanol as an alternative to bioethanol. The fermentative butanol production is deemed uneconomical because of high substrate costs, butanol toxicity, low production rates from batch process and energy intensive downstream processing. The development of an alternative, highly productive and feasible butanol production process was investigated in this work. A novel two-stage fermentation process, coupling continuous (first stage) and repeated fed-batch (second stage) operated fermenters was developed and shown to be superior to batch, fed-batch and two-stage continuous fermentations reported based on high volumetric and specific productivity of 1.47 g/L/h and 0.62 g/gCDW/h respectively. Due to butanol toxicity which limits the concentration in the fermentation broth to 12 g/L, gas stripping was integrated to the fedbatch fermenter to remove butanol from the medium. As proof of principle, pervaporation operated ex situ, was also investigated and compared to gas stripping for product removal. Gas stripping and pervaporation not only function by preventing cells from coming into contact with toxic butanol concentrations but also as solvent pre-concentrations steps before final downstream solvent separation. Butanol concentrations up to 59 g/L and 167 g/L were obtained from gas stripping and pervaporation respectively. The ”operating window” tool was used to evaluate the feasibility of the existing butanol fermentations and to identify the most favorable process configurations. These were identified as processes which combine cell immobilization and in situ product removal with either fed-batch or continuous fermentation. The developed process with achieved productivities belongs to the most favourable process configuration. Scaling up this process to an industrial plant with 132 kT/year butanol production shows that a combination of continuous and fed-batch fermentation with in situ gas stripping and distillation results in an economically sound process as compared to the historical batch process combined with distillation. The total capital required for this process is $133 million with butanol production cost at $0.58/kg. As compared with $0.44/kg butanol production cost from petroleum there is still a big margin to cover by the current biotechnological production routes to compete with the chemical process.
Nákup knihy
Development of a novel two-stage butanol production process: integrating continuous and fed-batch fermentation, Mpho Setlhaku
- Jazyk
- Rok vydania
- 2014
Doručenie
Platobné metódy
Nikto zatiaľ neohodnotil.