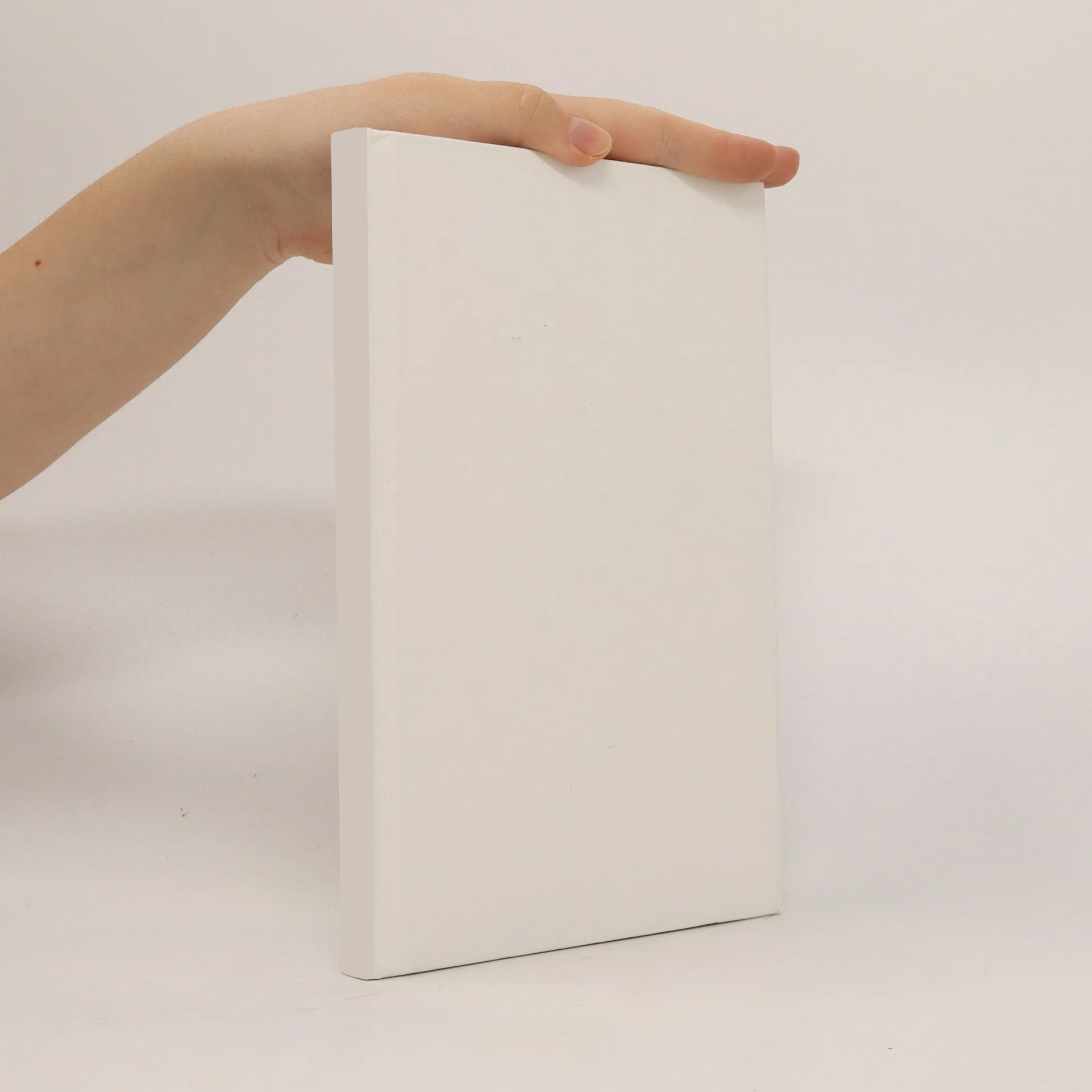
Simulation of thermo-chemo-mechanical coupled additive manufacturing processes using peridynamics
Autori
Viac o knihe
In the health care industry the treatment of neural hearing loss with cochlear implants is a well-established medical intervention. Since only standard implant sizes are available, a patient-specific Additive Manufacturing (AM) process to improve their functionality is desirable. Therefore, a prototype 3D-printer device for the manufacturing of Room Temperature Vulcanisation (RTV) medical grade silicon was built by the Excellence Cluster Hearing4all of Hannover Medical School. However, a comprehensive understanding of the material behaviour during the extrusion-based printing process does not exist and is currently not possible. The crucial point in the AM process is the material spreading during the curing being reduced by the application of laser radiation. As a result, a simulation driven support to capture the influence of processing parameters and to optimise the process is desirable. The objective of this work is the development of a numerical framework enabling the simulation of the underlying AM process in the sense of a proof of concept. Thus, a continuum mechanical large strain curing model is developed, which is capable of showing the curing specific phenomenological behaviour. In contrast to existing models the developed model includes an extension to finite plasticity to relate the spreading of material in the uncured state to dissipative behaviour. Furthermore, a meshfree discretisation of an enhanced peridynamic correspondence formulation, based on subdivisions of the influence domain to prohibit arising instabilities in the deformation field, is implemented as a numerical solution. Due to the application of the developed local material model within the non-local theory of Peridynamics, local-non-local coupled equations for the equation of motion and the energy equation arise. Furthermore, the specific laser impact and convective boundary conditions are modelled within the energy equation by volumetric heat source terms. In numerical examples the capability of the enhanced correspondence formulation for simulations at large strains is shown. Moreover, the plasticity in the developed large strain curing model appears to be well-suited for the modelling of material spreading in the fluid-like state. Additionally, the thermo-chemo-mechanical coupled behaviour of a reduced material spreading with respect to the application of higher temperatures resulting in an accelerated curing is verified. Finally, simulations of the material extrusion are performed, whereby in the final simulation of the complete AM process a reduced material spreading due to the application of laser radiation is observed. The results are overall in line with the modelled phenomena and expected behaviour. Consequently, a successful proof of concept of the simulation of the AM process is performed and it is desirable to add additional physical effects in the developed framework.