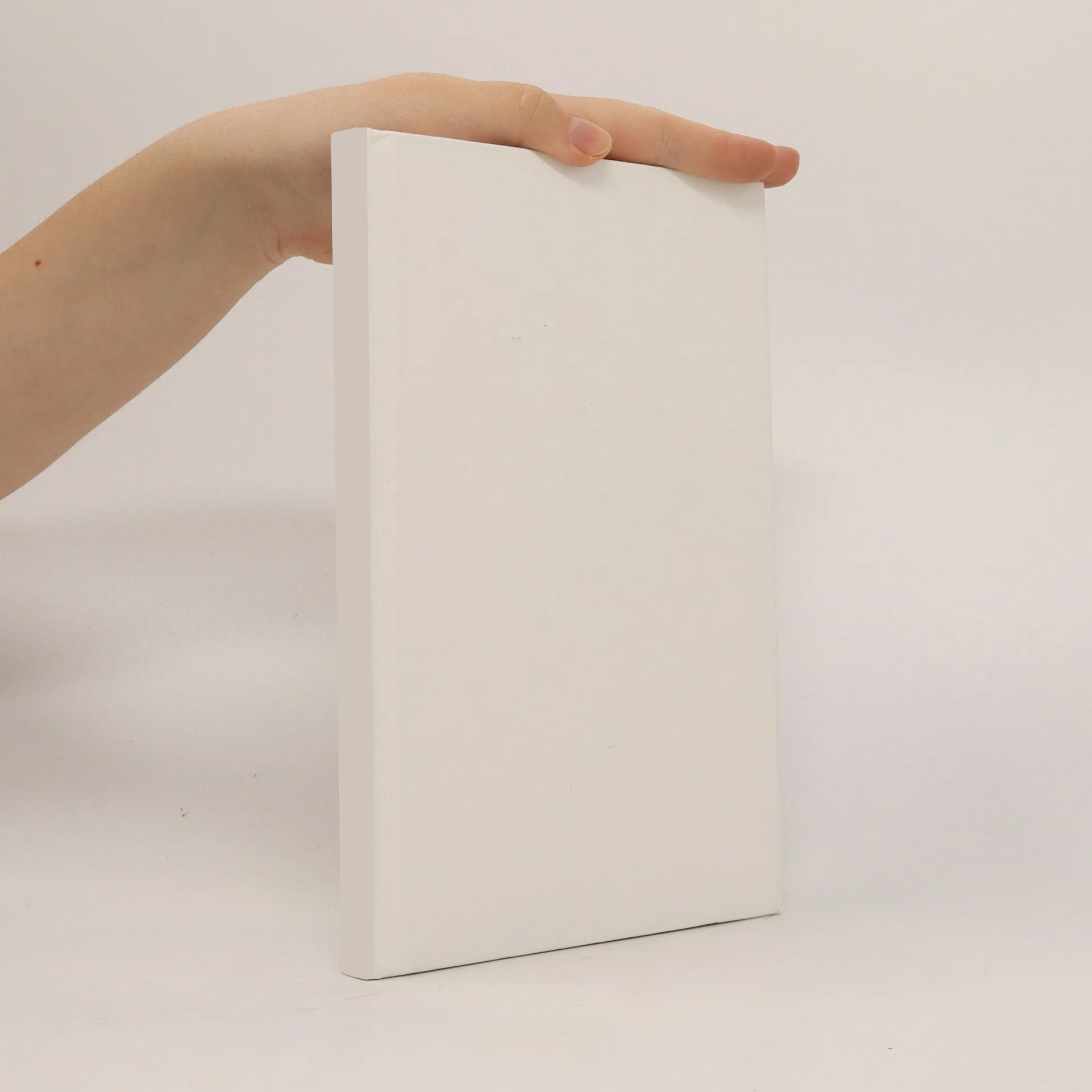
Cost efficient production process of automotive interior textiles using weft knitted spacer fabrics
Autori
Viac o knihe
Automotive interior textiles need to last the lifetime of the car. The demands regarding durability and comfort are high. Next to the mechanical properties, the recycling of the textiles is important. Door panels, headliners and seat cover textiles are build-up of a composite material. The surface structure is either a textile or leather material. This structure is laminated onto a PUR-foam or a non-woven structure. This multilayer structure cannot be properly recycled. Moreover, the breathability of these composites is limited due to the PUR-foam. Within this thesis a new, economic competitive textile spacer fabric is developed that can be used as a substitution to the conventional textile/foam composite structures. Spacer fabrics consist of two parallel textile layers that are connected through pile yarns. The pile yarns keep the distance between the two layers. Due to this structure, spacer fabrics possess higher climate comfort properties than regular foam composites. The whole spacer fabric can be produced in one process step and consists only of polyester. Therefore, it is recyclable. To achieve the required properties of conventional automotive fabrics, the „Textile Development Method - TED“ for the systematic development of spacer fabrics is established. With this, new and suitable patterns are developed and evaluated for the use in the automotive interior. The method is implemented and validated for two sample components, a seat cover fabric and a headliner fabric.