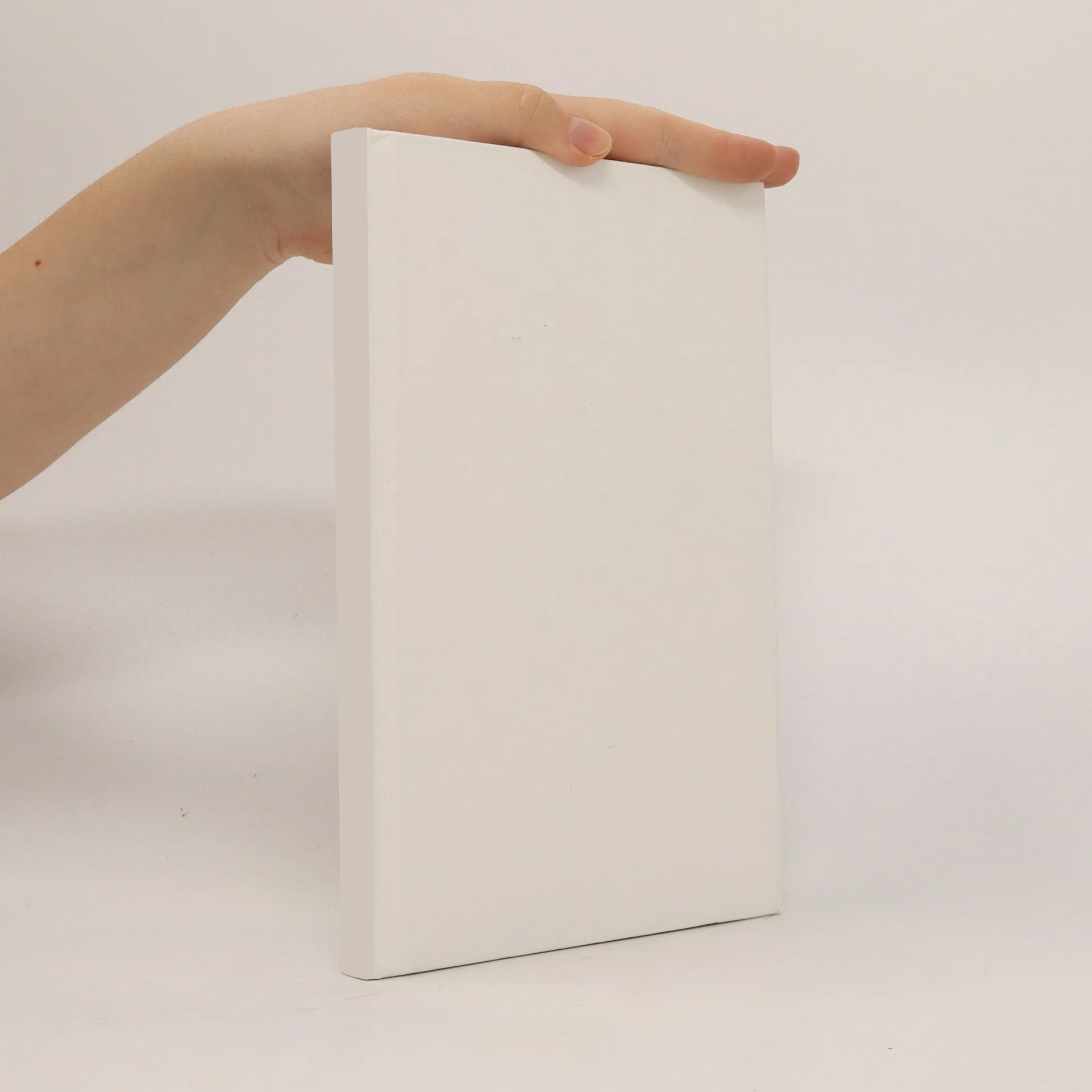
Smoothed particle hydrodynamics for ductile solids
Autori
Viac o knihe
This work is concerned with the development and application-oriented validation of a numerical simulation model for ductile solid continua based on the meshless Smoothed Particle Hydrodynamics (SPH) method. Thereby, it makes a contribution to the extension of the current portfolio of computer-aided engineering analysis techniques that allow to reliably predict the macroscopic behavior of ductile solids experiencing extreme deformations, major changes in the system topology, material failure including structure disintegration and/or a large number of contacts occurring at the same time. In order to achieve the aforementioned goal, the original SPH method for solids needs to be variously extended. One of these extensions is the presented linear thermoelastoplastic coupling. To be able to accurately reproduce the plastic as well as the failure behavior of a real material in the simulation, the Johnson-Cook flow stress and damage model are further incorporated. On top of that, simple but proven concepts to solve the SPH-inherent problems of particle clumping, numerically-induced fracture and a reduced results quality close to the free surfaces of a model are integrated into the developed formulation. Finally, the possibility to dynamically adjust the local spatial discretization is introduced, which helps to reduce the required numerical effort. Having made all the afore-described modifications to the original SPH method for solids, the focus is on the qualitative and quantitative validation of the extended variant in the context of complex industrial applications. Here, the manufacturing processes of Friction Stir Welding and orthogonal cutting serve to demonstrate the ability of the developed SPH model for ductile solids to correctly simulate such challenging scenarios.