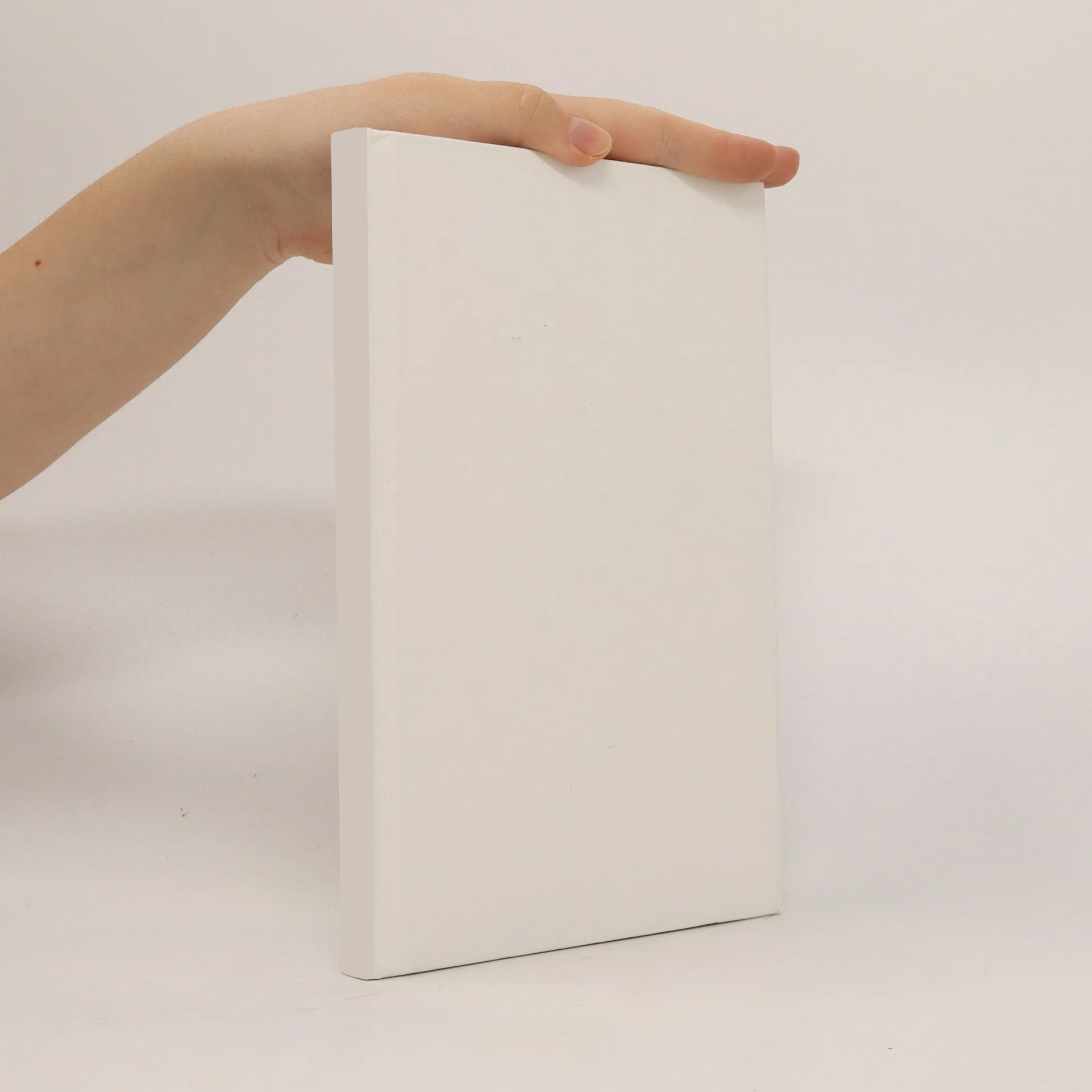
Parametre
Viac o knihe
WC-Co cemented carbides (hardmetals) are a group of composite materials exhibiting outstanding combinations of hardness and toughness. As a consequence, they are extensively used for highly demanding applications, such as cutting and drilling tools, where cyclic loading is one of the most critical service conditions. The micromechanics of fracture in hardmetals under static loads is well investigated and understood. Studies regarding failure by fatigue on the other hand, is mainly limited to experimental investigations conducted at a component scale and seldom refer to the influence of microstructure on the failure mechanism. Moreover numerical studies evaluating the mechanisms of fatigue crack growth in hardmetals is also scarce. Experimental observations indicate that the overall fatigue performance of hardmetals can be predicted from the early stages of the microcrack evolution. Taking this into consideration, a numerical methodology for evaluating the fatigue crack propagation in hardmetals was developed. Within this context, a model based on a continuum damage mechanics approach together with an element elimination method was implemented in a commercial finite element software for simulating the crack propagation in the material. In order to validate the approach used, numerical models based on both the real (damaged) and artificial microstructures was generated. It is found that, proposed model is capable of capturing damage evolution with cyclic loading in WC-Co, as numerical results reflect satisfactory agreement with real crack pattern resulting from experiments.
Nákup knihy
Finite element simulation of fatigue crack growth in hardmetal, Utku Ahmet O. zden
- Jazyk
- Rok vydania
- 2015
Doručenie
Platobné metódy
Navrhnúť zmenu
- Titul
- Finite element simulation of fatigue crack growth in hardmetal
- Jazyk
- anglicky
- Autori
- Utku Ahmet O. zden
- Vydavateľ
- Shaker Verlag
- Rok vydania
- 2015
- ISBN10
- 3844040986
- ISBN13
- 9783844040982
- Kategórie
- Skriptá a vysokoškolské učebnice
- Anotácia
- WC-Co cemented carbides (hardmetals) are a group of composite materials exhibiting outstanding combinations of hardness and toughness. As a consequence, they are extensively used for highly demanding applications, such as cutting and drilling tools, where cyclic loading is one of the most critical service conditions. The micromechanics of fracture in hardmetals under static loads is well investigated and understood. Studies regarding failure by fatigue on the other hand, is mainly limited to experimental investigations conducted at a component scale and seldom refer to the influence of microstructure on the failure mechanism. Moreover numerical studies evaluating the mechanisms of fatigue crack growth in hardmetals is also scarce. Experimental observations indicate that the overall fatigue performance of hardmetals can be predicted from the early stages of the microcrack evolution. Taking this into consideration, a numerical methodology for evaluating the fatigue crack propagation in hardmetals was developed. Within this context, a model based on a continuum damage mechanics approach together with an element elimination method was implemented in a commercial finite element software for simulating the crack propagation in the material. In order to validate the approach used, numerical models based on both the real (damaged) and artificial microstructures was generated. It is found that, proposed model is capable of capturing damage evolution with cyclic loading in WC-Co, as numerical results reflect satisfactory agreement with real crack pattern resulting from experiments.